一、项目简介
厦门某半导体企业是具有国际影响力的全色系超高亮度发光二极管外延及芯片生产厂商,总部坐落于美丽的厦门,产业化基地分布在厦门、天津、芜湖、泉州等多个地区,是国家发改委批准的“国家高技术产业化示范工程”企业、国家科技部认定的“半导体照明工程龙头企业”,承担国家“863”、“973”计划等多项重大课题,并拥有国家级博士后科研工作站及国家级企业技术中心。
该企业主要从事全色系超高亮度LED外延片、芯片、化合物太阳能电池及Ⅲ-Ⅴ族化合物半导体等的研发、生产与销售,产品性能指标居国际先进水平。目前拥有1级到100级的现代化洁净厂房,上万台(套)国际最先进的外延生长和芯片制造等设备。公司凭借强大的企业实力,实现了年产外延片2400万片、芯片3000亿粒的生产规模,占到国内总产能的58%以上。2014年,公司进一步扩大和延伸LED产业链建设,在厦门投资新建的LED产业基地和通讯微电子器件项目,使公司的生产规模直接迈入国际顶尖行列,并成为国际上具备规模化生产、研发化合物半导体芯片能力的企业。
为适应公司快速发展和打造LED芯片产业龙头和智能化标杆,公司启动了数字化工厂战略,并选择了北京mile米乐体育平台官网科技有限公司作为数字化工厂整体解决方案战略合作伙伴,共同推进战略落地,以数字化工厂业务咨询为基础,以产品研发和芯片制造业务主线,以信息集成为技术手段,建设支撑产品生命周期全过程的数字化统一平台,实现研发过程中管理信息、需求信息、研发信息、制程信息、资源信息、制造信息、质量信息等基于标准化的有效整合和管理,在数字化统一平台上,建立全球研发协同体系、实现产品全球研发和制造的高效运行模式,有效提升企业的管理能力、研发能力、制程能力、制造能力、协同效率和快速反应能力,增强企业的核心竞争力。
二、项目实施方案:
在客户现行信息技术应用的基础上,以业务发展需求为导向,遵循基本原则:“统一规划、统一组织、统一标准、统一平台、统一管理”,简称“五统一原则”,针对客户战略,此项目遵循如下实施原则:
• 业务牵引,需求驱动:数字化工厂建设将以工厂业务需求为发启,通过工程化的推进管理模式,分阶段推进数字化工厂建设。在推进过程中,特别要重视需求调研和需求分析,只有完整准确的需求调研才能做好数字化工厂建设。
• 统筹规划,突出重点:数字化工厂建设涉及的业务面广而复杂,而资源是有限的。在推进数字化工厂建设过程中,需要在一定时期内以有限的资源,根据统筹规划和数字化工厂规划,确保以科研生产管理平台为重点的管理信息化建设落实。
• 注重协同,加强集成:在建设数字化工厂前应该充分考虑各系统之间的集成,统一数据源。同时在数据共享的情况下注重各部门各业务的协同。
• 完善基础,深化应用:在完善网络与硬件基础的同时,通过数据规范、标准配合、制度约束的方式构建扎实的数字化工厂数据基础,并在此基础上开展深化应用工作,分析评估基于数字化工厂的科研生产管理,从而解决瓶颈问题、优化流程。
该数字化工厂项目实施方案包括数字化顶层设计、数字化研发、数字化制造管理和EAP机台自动化及落地实施。
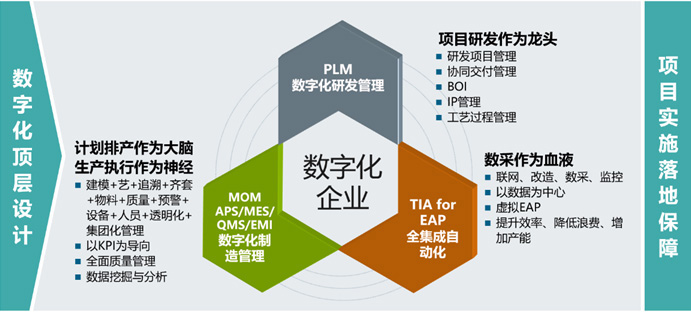
图1 项目实施方案及框架
• 数字化顶层设计:mile米乐体育平台官网对客户当前业务模式、业务流程、管理瓶颈及信息化现状进行综合诊断和优化,同时结合行业内标杆企业智能制造最佳实践经验,采取顶层设计与咨询分模块详细设计分阶段实现持续性变革管理,这一标准化路线图,实现客户数字化工厂的顶层咨询规划与落地。
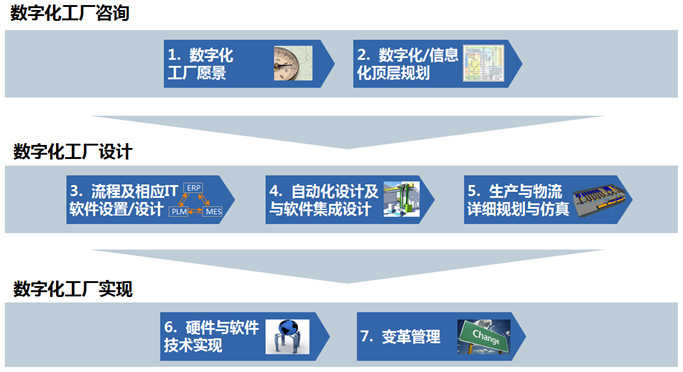
图2 数字化工厂项目咨询方法
•数字化核心解决方案:客户数字化解决方案由数字化研发、数字化制造运营管理和EAP组成。首先通过PLM建立全球协同研发平台,实现LED芯片研发创新,然后MES构建企业级的芯片制造管理平台,通过这一层的MES系统实现的自动/柔性化生产线和的PLM和ERP连接和贯通,最后通过机台连线自动化(EAP)建立工业网络,实现设备监控与数据采集及生产线自动化。
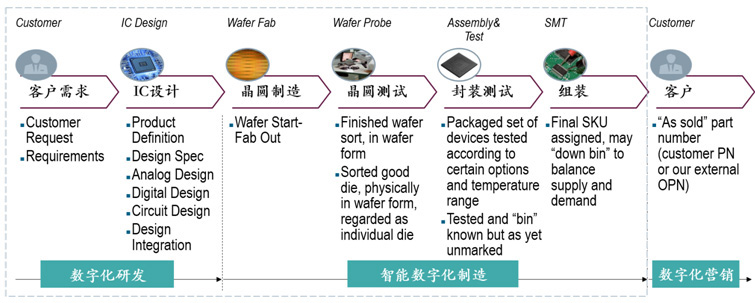
图3 数字化实施方案
三、技术路线:
基于客户构建智能工厂的长远愿景,参考国际标准ISA-95对企业架构层级定义,客户数字化工厂项目将全面构建各个层级的能力,分层次打造全新的数字化工厂。客户数字化工厂将通过制造评估和工艺设计、生产运营管理、全集成自动化控制以及生产线的构造,开展业务活动并协同工作。
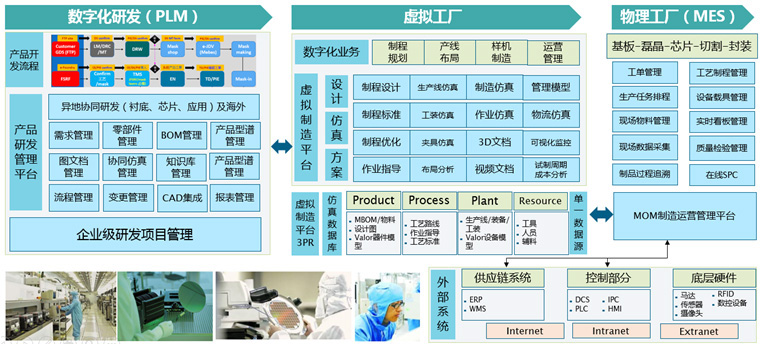
图4 数字化技术架构
(1)企业层 & 管理层:主要是产品研发PLM和企业管理ERP层面。尤其是应用PLM中的数字化制造技术,实现工厂的数字化建模和仿真分析,并基于虚拟工厂展现和操控生产。为数字化工厂奠定基础,通过产品全生命周期的数字制造和虚拟制造实现工程信息化,通过ERP和综合管理平台打造管理信息数字化。车间层的技术与生产管控方面,通过工艺评估、工艺设计及仿真实现工厂的指导思想的数字化,通过工厂规划建立支撑车间优化和产线优化,通过生产运营管理,达到实现生产订单、在制品、质量、设备利用率、物料等全方位管控。
(2)操作层:主要是执行和发布各种生产指令;实现产品、工艺、设备、测量仪器等各种数据的传递和采集。
(3)控制层 & 现场层:主要是接收操作层的指令,来实现现场层的各种硬件的自动化控制和驱动,确保其准确执行。现场部分主要是生产线现场的各种设备、工装、工具、测量仪器和物流设施等各方面的内容。
四、项目成果:
此项目取得了以下八大成果:
序号 | 八大能力 | 成果描述 |
1 | PLM | 运用PLM解决方案来驱动企业价值链的纵向及横向集成 |
2 | R&D Trailblazer | R&D的设计过程中,通过对工厂所有的设备、在制品的状态,都有全面的了解及分析及模拟,对潜在有问题的步骤进行预判,减少等待及维护步骤的发生频率来缩短产品研发时间 |
3 | Ecosystem Modeling Simulation | 通过在系统里进行虚拟建模来优化工厂布局 |
4 | Decision Tree | 对工厂所有运营及成本数据进行跟踪及分析,找出节约成本的机会,提升工厂运营效率 |
5 | Forward-look Process Management System | 对Wafer的每个生产步骤及工业流程进行全方位跟踪,通过预防式维护及Decision Tree等方法去主动发现潜在的风险,规避问题的发生 |
6 | Yield Management | 通过自我完善体系,对生产流程及不同可选方案进行分析及学习,不断完善自我判断能力,是系统在某个生产环节发生故障时能给出相应的备用方案 |
7 | Big Data Based Architecture Design | 通过打造一个以大数据及云计算为架构的智能制造生态体系来实现企业在其价值链上端到端的集成及协同 |
8 | Equipment Automation Program | EAP作为设备的底层接口负责生产设备之间的连接以及设备中各数据包括生产数据的运行 通过设备自动化 (EAP) 提升生产效率 |
五、帮助企业实现了:
(1)优化业务流程,提升业务效率:实现研发和制造业务一体化、生产过程透明化,具有全球协同研发、制程设计结构化、车间排产动态化、生产反馈实时化的支撑能力,实现知识管理,累积产品设计诀窍,提高知识重用率,支撑形成精益文化。
(2)通过全球协同研发平台,提升产品创新管理能力:对以项目计划为主线、产品为核心,建立可视化的数字化协同研发环境。实现对产品设计、器件采购、工艺准备、生产技术准备和生产执行进行管理,包括多项目计划的管理、产品设计进度、物资采购进度、工艺准备进度、生产准备进度和生产进度的可视化监控,实现实时管理、集中反馈、统一决策的科研管理信息流处理机制,为企业决策支持服务,有效处理多项目管理能力。
(3)通过精细化的车间现场管理环境,提升数字化车间执行能力:建立数字化制造现场管理平台,构建车间资源、计划、执行、控制全面管理和控制的精细化和可视化的车间现场管理和监控环境。实现包括车间生产计划、生产过程监控、质量管理、设备运行状态分析、工具工装管理、车间数据采集、生产过程管理、看板管理、统计分析、产品追溯管理、生产经营与绩效管理、报表管理等内容管理。实现生产过程实时监控与优化、完善制造资源分配、提高资源利用率、优化配置以及与其他系统之间的数据传递,达到生产前规划、生产中监控、生产后追踪的全方位支撑,提升研究所的数字化制造能力。
六、实施成效及经验总结:
项目为企业带来了如下具体指标的优化。
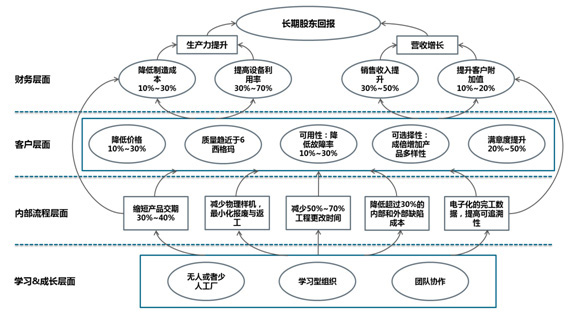
七、数字化工厂项目经验总结:
(1)重视数字化工厂顶层设计与规划:由专业的方案顾问梳理与规划顶层架构。
(2)夯实数字化企业平台:一方面进行端到端价值链整合(整合PLM、ERP、MES和CRM系统,厘清产业价值链实施PLM系统,实现虚拟设计和开发;另一方面实现网路化的纵向集成,打造数字化工厂(实施MES/WMS系统,建立工业4.0的核心系统与框架,打通SCADA、EAP、WCS与MES、WMS的整合,提升工厂的自动化运作程度)。
(3)完善决策与计划平台:监控/报表/看板体系完善与移动化应用、大数据平台建立与整合、先进产能计划与线上排程规划等。
(4)项目持续升级及优化:智能工厂不是目的,其目的为提升产品竞争力与质量智能工厂,无法一蹴而就,需要企业长期的努力与变革。